Tailored Product Packaging Devices Repair Solutions to Suit Your One-of-a-kind Service Requirements
In today's competitive market, organizations should guarantee their product packaging operations run perfectly, and customized repair services for devices are pivotal in achieving this. This conversation aims to uncover the nuanced advantages of personalized repair service methods.
Understanding Your Tools Demands
To efficiently attend to the repair service and upkeep of product packaging equipment, it is vital to gain a thorough understanding of your tools needs (packaging equipment repair services). This entails evaluating the certain types of equipment being used and identifying their roles within your manufacturing line. Acknowledging these elements enables you to focus on maintenance jobs and assign sources successfully, decreasing downtime and guaranteeing smooth operations
An in-depth inventory of your tools, including make, upkeep, age, and version background, creates the keystone of this understanding. This information facilitates informed decision-making relating to fixings and upgrades, making certain that interventions are both prompt and cost-effective. Furthermore, recognizing the functional demands placed on each piece of equipment assists in predicting deterioration patterns, therefore enabling more accurate organizing of preventative maintenance.
Collaborating with experienced technicians who can supply expert assessments and suggestions is likewise essential in refining your devices administration approach. Ultimately, a comprehensive understanding of your tools requires not only optimizes performance however likewise prolongs the life-span of your equipment, guarding your financial investment.
Benefits of Personalized Repair Service Solutions
Personalized repair service solutions supply a tailored technique to fixing and preserving product packaging tools, making certain remedies that fit the distinct demands of each organization. This bespoke approach supplies myriad advantages, improving functional efficiency and minimizing downtime. By understanding the specific equipment and procedures of a business, personalized services can attend to problems better than generic solutions, guaranteeing that repairs are straightened with operational goals and workflow characteristics.
In addition, these solutions help with far better resource administration. Tailored fixing strategies help predict upkeep requirements, allowing services to designate sources more successfully and minimize unexpected prices. This positive approach not just lengthens tools life-span however additionally enhances performance, stopping frequent failures and fostering a more trusted production environment.
Furthermore, customized repair service solutions boost the flexibility of services to developing market problems. As packaging technologies breakthrough, having a repair work solution attuned to a business's one-of-a-kind setup makes sure quick adjustment to brand-new tools and procedures. This agility is critical for maintaining affordable advantage and consumer fulfillment. In addition, customized solution cultivates a closer connection with repair service providers, making sure quicker feedback times and more effective communication, eventually bring about improved service quality and company development.
Key Components of Tailored Solutions
A well-crafted customized option for product packaging equipment fixing is built upon several crucial components that ensure efficiency and integrity. A thorough analysis of the devices is important. This involves detecting the origin of any kind of functional issues and understanding the particular requirements of the machinery, which lays the groundwork for creating an exact repair work strategy.
Second of all, the usage of high-grade, suitable parts is paramount. Picking components that straighten with the original tools specs not only boosts performance yet likewise prolongs the life expectancy of the machinery. This interest to information reduces the risk of future malfunctions and ensures smooth operation.
An additional essential component is the application of a tailored maintenance plan. packaging equipment repair services. Precautionary procedures and normal assessments tailored to the devices's unique requirements can substantially decrease downtime and enhance performance

Integrating these components into a customized repair work solution not just addresses prompt concerns yet also gives long-term benefits, boosting general productivity and cost-effectiveness for companies.
Selecting the Right Company
Selecting the right provider for packaging tools repair service is a crucial decision look at more info that can substantially impact a company's operational efficiency and expense management. A trusted service supplier ensures timely repair work and upkeep, lessening downtime and avoiding potential manufacturing delays. When choosing a copyright, organizations need to take into consideration numerous essential aspects to guarantee they select a partner that lines up with their particular needs.
To start with, experience and experience in managing similar tools are crucial. A company with a tested performance history in the product packaging sector can supply solutions and understandings tailored to one-of-a-kind organization obstacles. Referrals and situation studies from previous clients can provide valuable proof of their capacities.
Secondly, review the service provider's responsiveness and availability. packaging equipment repair services. A perfect companion should offer flexible solution choices, consisting of emergency repair work solutions, to address urgent requirements quickly. This ensures very little interruption to operations and maintains efficiency levels
Additionally, think about the series of services offered. A comprehensive copyright must not only supply repair work but also precautionary upkeep and technical support. This holistic strategy can improve procedures and foster lasting partnerships.
Making Best Use Of Tools Lifespan
Efficient devices upkeep strategies are as essential as choosing the best service copyright when it comes to maximizing the life expectancy of packaging devices. Such proactive measures make certain that equipment functions at peak performance, thereby minimizing the threat of expensive downtime.
Additionally, buying training for your technical staff can considerably affect the long life of the machinery. Competent workers can identify prospective problems early, permitting for speedy corrective activities. This not just enhances the life-span of the devices yet additionally improves overall efficiency. Maintaining comprehensive upkeep documents is essential. These logs supply insights into reoccuring problems and assist in planning future maintenance activities a lot more efficiently.
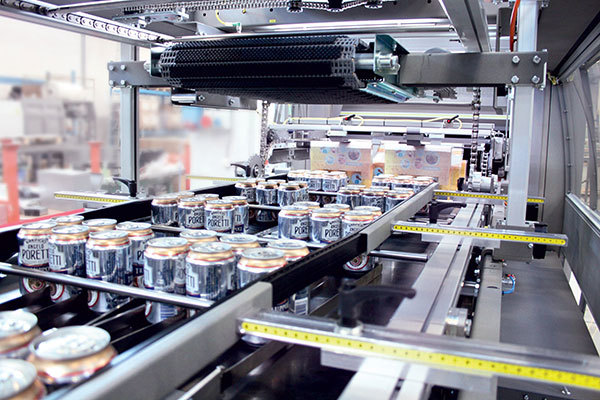
Final Thought
Customized packaging tools fixing solutions play a vital function in boosting operational efficiency and lowering downtime by straightening repairs with specific workflow dynamics. These customized options use top notch, compatible parts and positive upkeep strategies to expand equipment life expectancy and enhance performance. By promoting close relationships between businesses and provider, customized solutions enhance service top quality and lower expenses. Choosing the appropriate provider makes certain the review effective execution of these solutions, eventually leading to considerable long-lasting advantages for companies.
In today's competitive market, services have to guarantee their packaging procedures run flawlessly, and tailored repair services for devices are essential in accomplishing this.To properly address the repair and maintenance of packaging tools, it is vital to gain a comprehensive understanding of your equipment requires.Personalized repair services use a customized method to fixing and preserving product packaging devices, ensuring services that fit the unique needs of each organization.Reliable equipment upkeep approaches are as crucial as selecting the appropriate service copyright when it comes to maximizing the life-span of product packaging devices.Customized packaging equipment repair service solutions play a crucial duty in boosting operational effectiveness and reducing downtime by aligning fixings with certain operations characteristics.